Ship ahoy! It does not always have to be the metro, Vienna has much more to offer. This time we drop anchor at the “Stadtstraße”. The 3.2 km long street is to be built in “Donaustadt” and will connect “Seestadt Aspern” with the highway “Südosttangente”. What is unique about it is that almost half of it is tunnelled underneath, so due to the high groundwater level, a lot of the construction work must take place underwater.
*****
Engineer and digitalisation expert Sebastian Gerhard from ZÜBLIN Spezialtiefbau and Philipp Eder, who is responsible for the project on behalf of the eguana team, are telling us why anchors are essential for this and how exactly we are supporting the project with SCALES.
Half of the “Stadtsraße” that is to be built runs at a low level and has two tunnel constructions: the “Emmichgasse” tunnel and the “Hausfeldstraße” tunnel. “It is one of the major projects in Vienna,” explains Gerhard. “This means that many trades are busy at the construction site at the same time, and despite the large extension of the construction sites, space – as it is so often the case – is limited.”
The two tunnels are therefore being built using the so-called cut-and-cover construction method: In this civil engineering method, bored pile walls are first constructed. The cover of the tunnel is concreted onto these walls. Then the excavation takes place under the existing cover. This means that the surface of the ground can be driven over again quickly, which is very desirable in the narrow, urban area. “One of the biggest challenges in constructing the tunnels is the high groundwater level. This means that the tunnel structure must be tight and secured against buoyancy. Now here is our part of the game. We build a back-anchored sealing sole. For this, micropiles are first produced that serve as anchors,” says Gerhard.
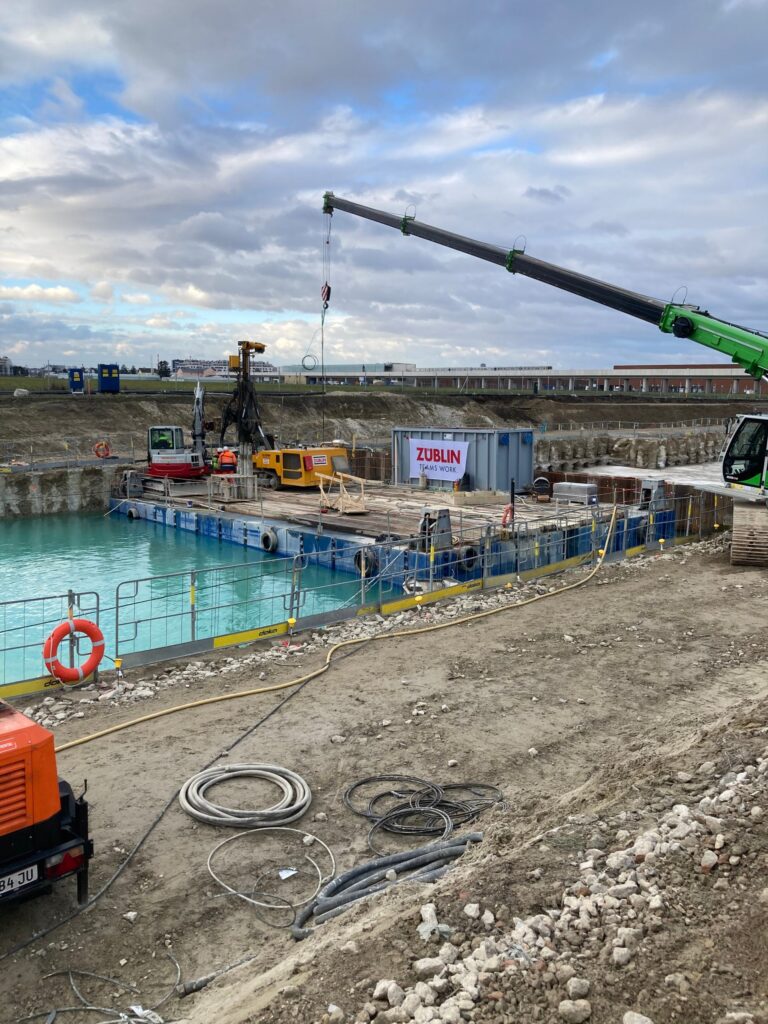
How does an anchor actually work?
Philipp Eder, an architecture student, knows how to explain complex construction topics simply – and in the case of a grouted anchor, how could that work better than with a regular anchor?
“By prestressing the anchor, the structure is secured against the forces of the ground. In our case, this is the ship that we want to secure with the anchor and the anchor chain – i.e., the tension member.”
The anchor keeps the ship from drifting away (or the construction element from sliding away). This requires traction – but not too much, because otherwise (as can be seen in the second illustration) the ship will be pulled under water (and the construction will collapse).
But if the anchor chain is too long, everything may seem fine at first glance (see figure 3), but with the next current the ship will drift away – and the insufficiently stabilised element will slip away at the first jolt.

Anyone can do “simple”
“The micropiles are then connected to a DSV or underwater concrete slab,” says Gerhard. This is how the soil for the tunnel is created. “The special aspect for us in this process is that we are working under further challenging conditions. The route is crossed twice by the underground and S-Bahn lines. In order to maintain railway operations, two steel auxiliary bridges were installed in advance, under which drilling is only possible at a limited height. This made it necessary to shorten the masts and our equipment had to be specially adapted for this unique operation. Due to the high groundwater, drilling from a work platform supported on rails and from floating pontoons is also necessary.
Water, anchor, what is missing to make the picture complete? Scuba divers, of course!
They were used, for example, to check the overgrowth from the anchor fill, to check the DSV and SOB wall and to install the head plates at the underwater concrete slab.
The vision was poor, said Gerhard, but the water surface looked very inviting at some points when viewed from above – just like in the Caribbean.

Gerhard emphasises: “We worked under enormous time pressure in the track bed of “Wiener Linien” during the track blockage in the summer holidays. Despite the lack of buffer time, we managed to be on schedule!
And there is another complication, because the micropiles must be installed very precisely in the subsoil, Gerhard explains. “This means that the Gewi bar cannot simply be “dropped”, as it is usually the case, but must be lifted into place by using an assembly bar. Since we are post-grouting the anchors, post-grouting hoses must be tied to the anchors in advance. These must not be damaged in order to allow for blasting with water and subsequent post-grouting with cement suspension.”
Maintaining an overview with SCALES
Around 6,000 anchors are needed in total for the project – and six production and injection protocols are created for each pile. It is not easy to keep track of everything.
The focus of eguana is the data management of injections. Since every anchor is related to an injection, it was obvious to also digitalise and visualise the technology and the related data flows. For this purpose, we developed a special input mask for the drillers together with “ZÜBLIN Spezialtiefbau” for the “Stadtstraße” project.
They only need to enter the corresponding data for the nine parameters. Nine parameters, that does not sound like a small number, nor is it – but it is much easier than entering them manually and evaluating them afterwards. Our logging in eguana SCALES then combines all logs fully automatically into one overall log. In this manner, we not only visualise the grouting pressure with which the anchor secures the construction, but also the type of anchor, the drilling depth, the material used and so on.
Through logging, “we are able to obtain the most precise and traceable information about the production of each pile. The digital data obtained originates directly from the device and its operator and can then be evaluated in a very uncomplicated way,” says Gerhard. Every performance is thus precisely documented and traceable, and the potential for errors is minimised.
All easy, one might think. But there were still a few minor teething problems: “At the beginning, there was a problem where the logs were not automatically linked to each other, even though the numbering was obviously entered correctly,” says Gerhard. “After several hours of troubleshooting, it turned out that the letter O (Oscar) looked confusingly similar to the number 0 (zero) and the entry was indeed wrong.”
Dreams of the future
“Hardly anyone else does data management the way we do it,” Philipp Eder is aware. So, the fact that most workers have not yet come into contact with such a form of recording is hardly surprising. “There are logs for the clamping process, but not much else. It would be cool if we could do automatic recording here as well. Then we could really cover the topic in its entirety, from drilling to injection
to the clamping process.” According to Philipp, the only thing that is missing in most cases is the corresponding data logger.
Gerhard foresees the future of anchors in 3D models of the actual installation, including all relevant additional information. In the future, he believes, more machine data will be recorded in general, such as drilling depth recording. This will mean less input from the drilling foreman. An automatic 3D as-built model of the fabricated anchors, which can be further used in the builder’s BIM model, would be another step towards digitalisation.
*****
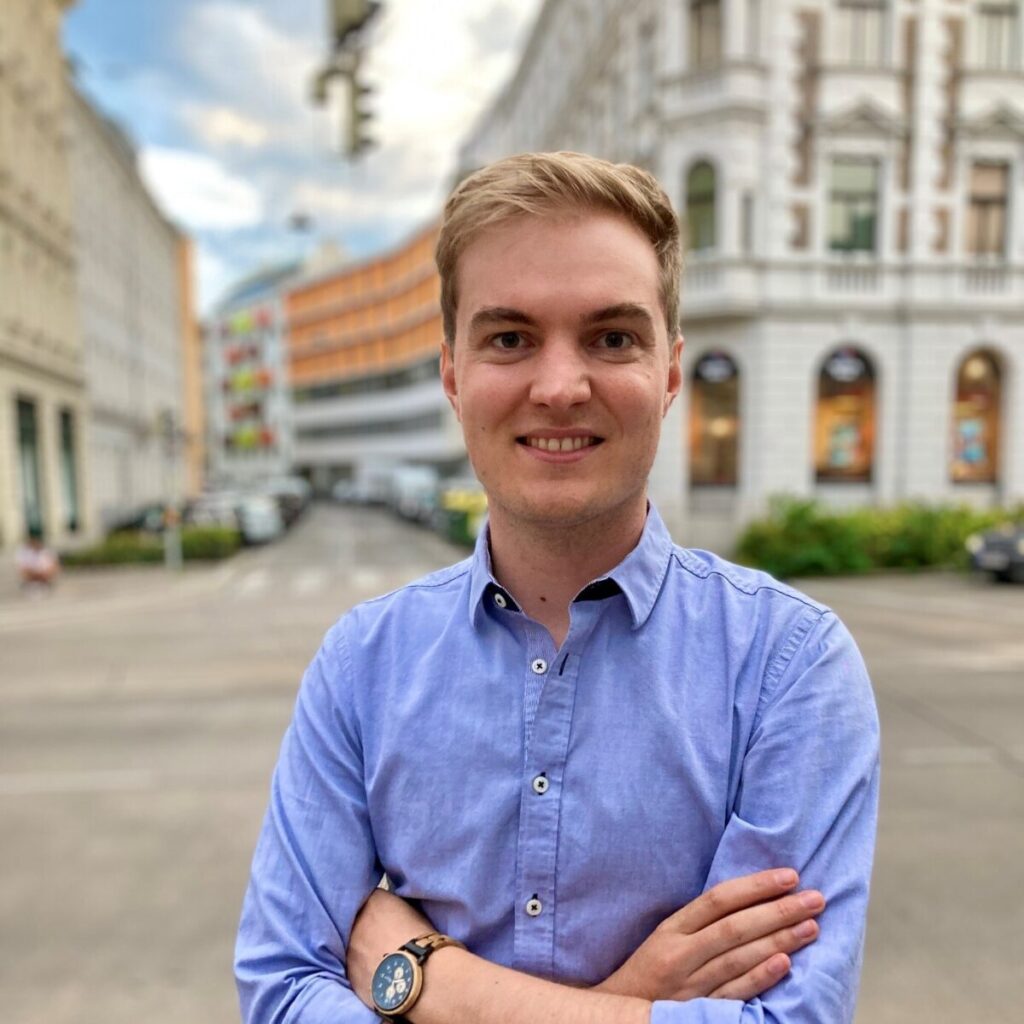
About Sebastian Gerhard
Born and raised in the south of Munich, the Züblin engineer came to Vienna back in 2010 to study civil engineering. According to Sebastian Gerhard, his father, also a civil engineer, is not entirely innocent of his fascination with construction sites, which has not failed to captivate him since his earliest childhood.
But he also remains busy apart from the “Stadtstraße”: Swimming, cycling, tinkering with his moped and crafting with 3D printing – plus, the native Bavarian bakes not only pretzels, but also good Italian pizza!